“Safety brings first aid to the uninjured.” The ultimate goal for the construction industry is to reduce workplace accidents, injuries, and deaths to zero. The fewer accidents there are, the more popular the construction industry will be. The only hope of reducing the number of accidents is to keep workers aware of safety issues, train them on these issues, communicate and discuss ways to improve these safety programs and concerns, and document these issues. In addition to these steps, workers must have the right equipment, must have proper supervision, must be innovative in finding ways to solve this problem, and must be transparent if such a problem does occur. The construction project manager has a significant responsibility to ensure safety in a construction site. 21.1% of all private industry deaths are in construction. Mainly the concentration should be paid to keep workers injury-free. Also, there are significant costs associated with an unsafe worksite.
What are the accidents that can happen during construction?
Accidents in a construction site can happen due to equipment failures, design ignorance, working carelessness, and natural disasters, etc. In addition, there are tunnel accidents, highway construction accidents, and residential building site accidents based on location.
Falling from height, crane or hoist accidents, slips and falls from stray tools and materials, being struck by falling objects, getting caught in or between objects, fires, and explosions, gas leaks, forklift accidents, electrocutions, chemical spills, trench collapses, defective tools and machinery, defective safety equipment, machinery accidents are some common accidents in a construction site.
How to manage safety in construction?
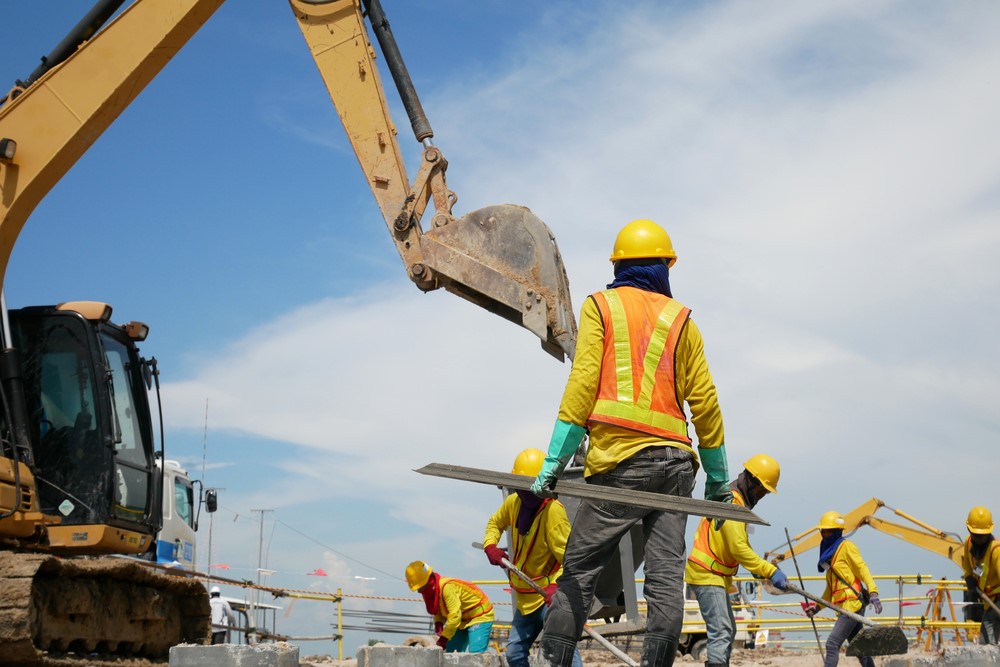
Even the fastest-growing construction companies also have the risk of major accidents. Construction accidents don’t just happen on their own, either. It’s usually the result of a series of events that ultimately led to the incident. When a construction worker is injured in an accident, it affects not just his life and livelihood, but also the future of the company. Construction accidents are largely preventable and companies should take every possible precaution to do their part in training, educating, and protecting their employees. A safety management system is a systematic way to identify hazards and control risks while maintaining assurance that these risk controls are effective.
Identification of workplace risk at the time of planning of work and implementation of suitable controls to avoid personal injury and property damage, monitoring of work to provide early detection and correction of unsafe practices and conditions, implementation of effective communication across all levels of the organization, protecting the adjacent public and private properties, providing safety education and incentive programs, complying with occupational, health, and safety rules and requirements are included in safety management. The safety risk assessment process for proper safety management in construction projects is,
Step 1: Identify Hazards.
Step 2: Assess the Risks
Step 3: Control the Risks
Step 4: Monitor/Review control Measures.
What is the responsibility of the construction project manager for safety?
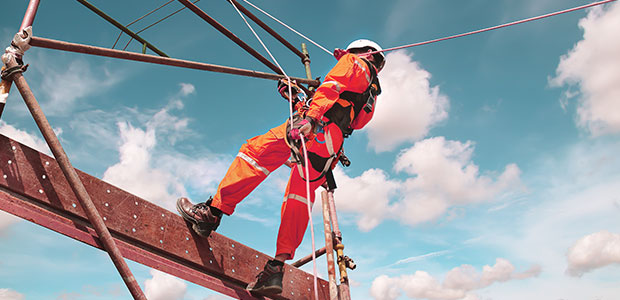
Worker safety should be a priority throughout any construction firm, regardless of its size. As a manager in this line of work, he/she has an obligation to understand the risks and keep workers safe on the job. First and foremost, a construction project manager must provide strong leadership. He must listen well to his crew and they must understand the role of the construction project manager and that he is actively working to keep them safe. Managing a team that embodies this concept will be beneficial to the organization as a whole. Management is responsible for providing the leadership and resources needed to implement effective safety and health programs.
Making worker safety and health a core organizational value, fully committing to eliminating hazards, protecting workers and continuously improving safety and health on job sites, providing sufficient resources to implement and maintain the safety and health program, visibly demonstrating and communicating their safety and health commitment to workers and others, setting an example through their own actions are some of the aspects of management leadership in safety and health which are the main responsibilities of business owners, managers, and supervisors.
What skills does a construction project manager should have to manage a construction site properly?
Employees need to be led by someone who has an in-depth knowledge of the construction industry. Successful construction project managers should be good in decision-making, problem-solving, leadership and supervising, planning and scheduling, cost estimating and analysis, understanding of legal practices. Possessing these skills and this knowledge will prove to be useful in managing a profitable and successful firm or project as well as a safe work site for all employees.
What is called Personal Protective Equipment and its importance?
PPE (Personal Protective Equipment) is equipment that will protect the user against health or safety risks at work. It can include items such as safety helmets and hard hats, gloves, eye protection, high visibility clothing, safe footwear, and safety harnesses. The purpose of PPE is to reduce employee exposure to hazards when engineering and administrative control are not feasible or effective to reduce these risks to an acceptable level. PPE is needed when there are hazards present. PPE has the limitation that it does not eliminate the hazard at the source and may result in employees being exposed to the hazard if the equipment fails.
What are the most frequently cited standards in construction?
- Scaffolding – fall hazards can occur when scaffolds are not used properly.
- Fall Protection (application, scope, definitions) – consider using aerial lifts to provide safer working surfaces for elevated platforms
- Excavations – Never enter a trench that is unprotected.
- Ladders – Avoid ladders with metallic components near electrical work and power lines
- Head Protection – Use safety net systems or body harnesses
- Excavations (requirements for protective systems) – Use a protective system for trenches 1 foot deep or greater.
- Hazard communication – Make information accessible to employees at all times in a language or formats
- Fall Protection (training requirements) – Use an effective employee training program for hazardous substances
- Construction (general safety and Health Provisions) – Construction workers should wear work boots with slip-resistant and puncture-resistant soles
- Electrical (wiring methods, design and protection) – Check all electrical tools and equipment regularly for defect
Keep it in your mind that tomorrow: your reward for working safely today. An ounce of prevention is worth a pound of cure.
Safety is not an intellectual exercise to keep us at work. It is a matter of life and death. It is the sum of our contributions to safety management that determines whether the people we work with live or death.
Written by:
G.G. Tharini Wickramathilake
Civil’18 batch